Способы повышения эксплуатационной надежности приморских сооружений: коррозия крепежа
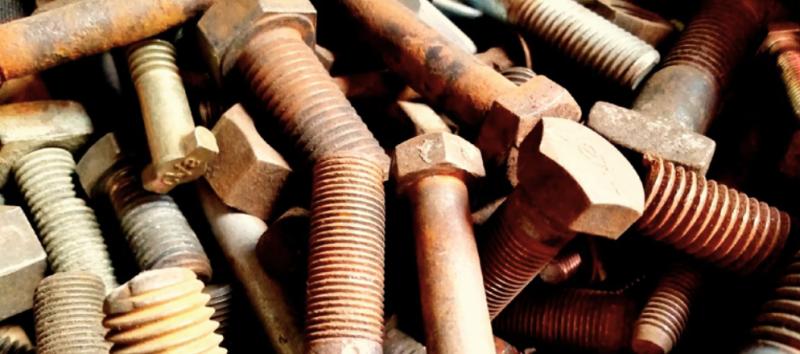
3,4 % мирового ВВП, по данным международной Ассоциации по защите и эксплуатационным характеристикам материалов (АМРР), составляют ежегодные потери от коррозии. Этот своеобразный «налог» платят все страны, и на него уходят триллионы: только в России, где такие потери достигают 3–5 % ВВП, ржавчина «съедает» как минимум 6 трлн рублей (исходя из объема бюджета в 172 148,3 млрд рублей, по данным Росстата).
Эти колоссальные потери можно сократить: согласно прогнозам, применение методов борьбы с коррозией способно снизить глобальные затраты на 15–35 %. Поскольку особенно остро вопрос стоит для конструкций и сооружений приморской зоны, именно здесь усилия по противостоянию разрушительным процессам дадут наибольшую отдачу.
Главным прокоррозионным фактором в зоне с морским климатом является наличие солей в воде, которая непрерывно воздействует на все конструкции и их элементы либо непосредственно, либо в аэрозольной форме. Высокие концентрации диссоциированных солей делают воду электролитом с высокой электропроводностью (около 2,5–3,0·10-2 Ом-1см-1 для общей солености 2–3 %). Это ведет к повышенной коррозионной активности хлор-ионов в отношении даже высоколегированных сталей, а для железа и низко- и среднелегированных пассивное состояние в морских условиях в принципе недостижимо.
«Исследования стального крепежа, которые почти 20 лет ведутся на острове Галоголанд в Северном море, показали, что скорость коррозионных процессов резьбового элемента в приморской зоне может быть от нескольких до десятков раз выше, чем в средней полосе России, — говорит Алексей Кисленко, представитель и технический специалист по ЮФО, ГК fischer. — Сегодня в связи с активным строительством портовой инфраструктуры, грузовых терминалов мы часто видим ошибки, которые допускают проектировщики из-за с недостатка опыта строительства в морском климате. До 80 % проблем со стальным крепежом связано именно с ошибочным его выбором, например с использованием оцинкованных элементов вместо нержавеющих».
Проблема эта интернациональна: например, несколько лет назад после внезапного разрушения винтов с торцевой головкой на заглушке цапфы шарового крана, расположенного на нефтяной платформе в Южной Атлантике (Тринидад и Тобаго), было проведено расследование причин аварии. Анализ показал, что кованые винты, соответствующие стандарту ASTM A574-17.6, были подвергнуты термообработке для получения закаленной мартенситной структуры и гальванически оцинкованы с толщиной покрытия 14,26 мкм.
Визуальный осмотр пострадавших винтов выявил, что разрушение началось на стыке головки и хвостовика, причем на этих же локациях исправных элементов, как показала макросъемка, также началось отслаивание покрытий.
Как выяснилось, около года крепеж эксплуатировался без надлежащего технического обслуживания, что привело к разрушению цинкового слоя и последующей деградации стали винтов. Увеличение твердости и снижение пластичности в нагруженных приложенным крутящим моментом элементах привели к образованию трещин (рис. 1), которые распространялись межкристаллитным образом по линиям наименьшего сопротивления до тех пор, пока головки винтов не обламывались без признаков деформации.
«В морской воде в силу ее высокой электропроводности коррозионная реакция катодного восстановления идет быстрее, — отмечает Алексей Кисленко, ГК fischer. — Образующиеся в ее процессе атомы элементарного водорода мигрируют непосредственно в тело детали, что приводит к охрупчиванию стали и ее разрушению под нагрузкой. Поэтому гальваническая обработка нагруженных стальных крепежных элементов, эксплуатирующихся в морском климате, не слишком целесообразна: покрытие быстро разрушается. В качестве первого выбора рекомендуется ориентироваться на изделия из легированных молибденом нержавеющих сталей (А2 или А4), лигандный состав которых обеспечивает лучшее сопротивление коррозии в условиях воздействия соленой воды. По наблюдениям, такой крепеж служит как минимум столько же, сколько конструкция целиком, то есть не менее 50 лет».
При этом использование оцинкованной стали целесообразно для собственно металлоконструкций, где используются крепежи, — это повышает общую устойчивость достаточно массивных деталей. Однако в этом случае выбирается сложная тактика защитных мероприятий, которая включает в себя применение качественного цинкования (уровень I и II-класса) и многослойной антикоррозийной обработки.
«Практика подтверждает, что скорость атмосферной коррозии оцинковки может в неблагоприятных условиях составлять до 20 мкм/год в морских и промышленных районах, — говорит Кирилл Ильин, проект-менеджер направления инженерных конструкций FACHMANN. — Поэтому при проектировании необходимо учитывать не только регион, но и конкретное место расположения объекта и условия эксплуатации: как далеко от береговой линии, направление преобладающих ветров, соленость воды и многое другое. Например, в приморской Ленинградской области для конструкций внешних блоков климатической техники предлагается цинковое покрытие, нанесенное горячим способом, которое обладает более высокой коррозионной стойкостью за счет большей толщины слоя. Для других ситуаций допускается гальваническое цинкование и/или порошковая окраска».
Таким образом, одним из ключевых факторов эксплуатационной надежности приморских сооружений становится состояние крепежа, который необходимо выбирать и эксплуатировать с учетом всех особенностей климата и условий работы, включая:
✓ использование крепежных элементов, исполненных из высоколегированных сталей;
✓ регулярные, не реже раза в полгода, осмотр крепежа и его замена по мере необходимости;
✓ дополнительные антикоррозионные мероприятия, предусмотренные регламентами.
Защита приморской инфраструктуры от процессов коррозии должна стать одним из ключевых элементов общих мероприятий по увеличению эксплуатационных сроков и снижению рисков. При этом нужно помнить: глобальные изменения, связанные с потеплением климата, по прогнозам ученых, уже к 2050 году могут привести к повышению уровня моря на 0,5 м, расширяя тем самым зону влияния прокоррозионных факторов.